La tecnología de impresión 3D se está convirtiendo cada vez más en una parte de cualquier práctica clínica, incluida la fabricación de ortesis de tobillo-pie (AFO). Quizá se pregunte si debería adoptarla en su consulta.
No hay una respuesta directa a esto. Es posible que la tecnología mejore cada día, pero aún así hay que tener en cuenta la eficacia, el proceso y los resultados tanto del AFO tradicional o hecho a mano como del impreso en 3D.
Por ello, hemos decidido poner la práctica clínica tradicional de fabricación de ortesis al lado del flujo de trabajo digital en 3D. Compararemos el tiempo, el flujo, los materiales y las herramientas utilizadas en ambos procesos. También hablaremos de lo que significa cada uno de ellos para su consulta.
He aquí un resumen rápido:
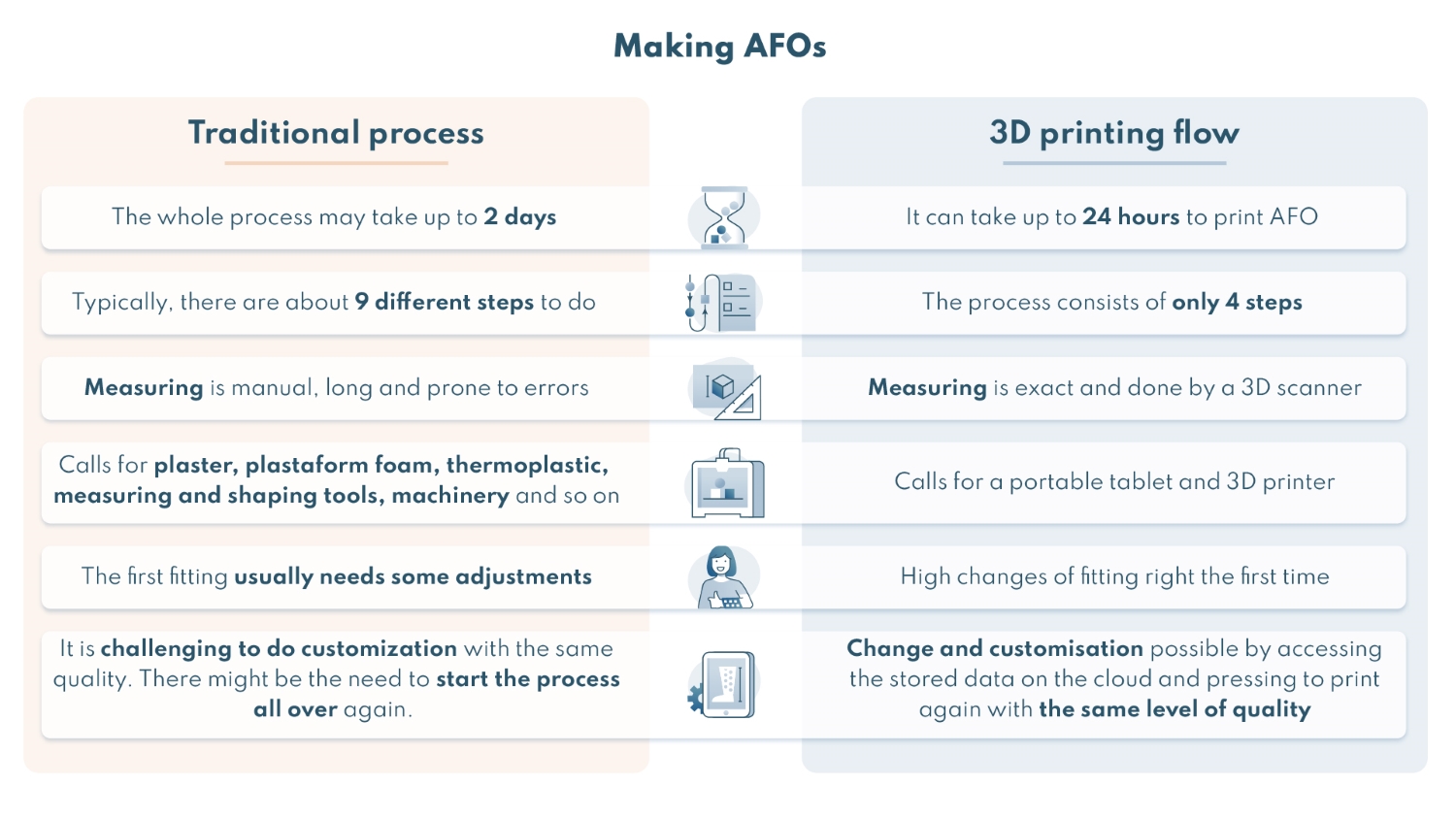
Fabricación de ortesis convencionales
Veamos el proceso típico de fabricación manual de ortesis:
1. Medición de
El proceso comienza con los técnicos ortopédicos que aíslan el miembro utilizando vaselina o papel de sánar para preservar el vello corporal a la hora de retirar posteriormente la impresión. La toma de medidas de la parte del cuerpo es el paso más importante. Sin embargo, sólo esto puede llevar hasta media hora, incluyendo la preparación y la limpieza.
2. Colocación de marcadores
A continuación, el técnico indica los marcadores óseos con un lápiz en la piel del paciente. A continuación, pega el tubo a la extremidad del paciente para utilizarlo como espacio de corte más adelante en el proceso.
3. Moldeado
Ahora viene el proceso de moldeado. En el caso de las ortesis complicadas, esto puede llevar hasta diez horas. Para dar forma a la impresión hay que cerrar la línea de corte con vendas de yeso y aislar el molde negativo.
4. Molde positivo y secado
A continuación, el técnico coloca una larga barra de acero en el centro de la órtesis para garantizar la estabilidad mientras rellena la impresión negativa con yeso líquido. Ahora tenemos un molde positivo. Una vez más, la impresión tiene que secarse, lo que tarda entre dos y cuarenta y ocho horas.
5. Corrección y pulido
El siguiente paso es corregir y pulir el molde positivo. Este puede ser un proceso arriesgado que puede disminuir la precisión del molde y potencialmente romperlo. Sin embargo, es un paso crucial en la preparación de la fabricación de las órtesis.
6. Eliminación del molde negativo
Una vez que la forma positiva está seca y lisa, el técnico ortopédico puede empezar a retirar el molde negativo. A continuación, se grapa el Plastazote o la espuma de plastaform sobre el modelo y se tira del termoplástico.
7. Calentamiento de termoplásticos
A continuación, el termoplástico se calienta en el horno. El horno hace que el material de PP, PE o copolímero sea flexible para que el técnico ortopédico pueda moldearlo sobre el modelo.
8. Eliminación del moho
Por último, el técnico retira el molde del modelo y alisa las asperezas.
9. Ajuste inicial
Es entonces cuando por fin estamos preparados para la colocación inicial de la órtesis. Normalmente son necesarios algunos ajustes, que pueden llevar algún tiempo. Cuando los ajustes que se necesitan son numerosos, puede resultar necesaria una órtesis completamente nueva. En esos casos, el técnico puede tener que volver a empezar el proceso.
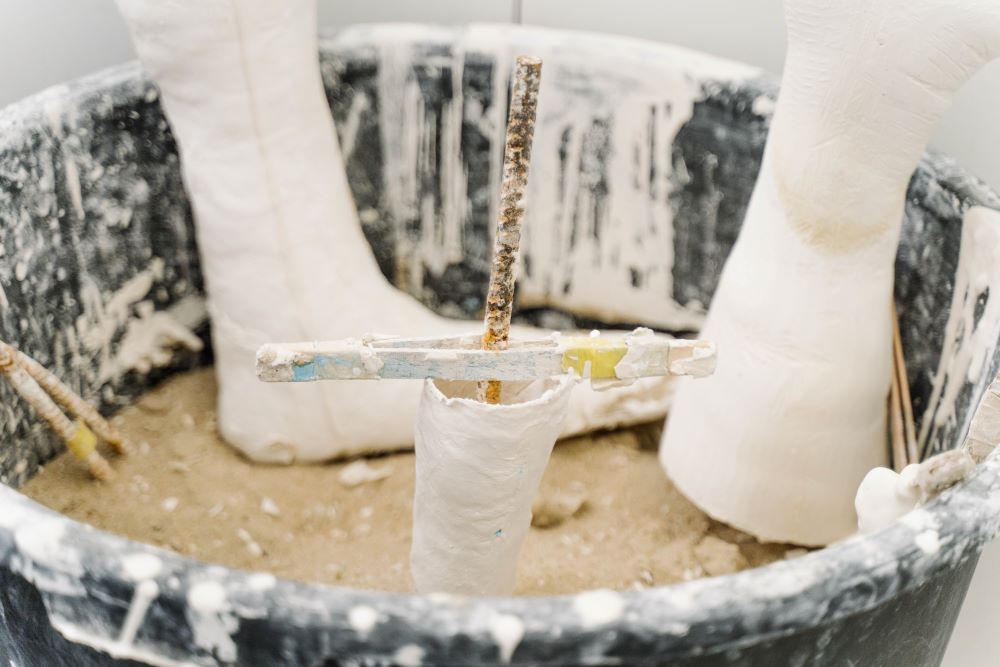
Es hora de compararlo con el flujo de trabajo digital en 3D.
Flujo de trabajo de las ortesis impresas en 3D
El proceso de flujo de trabajo digital consta de sólo cuatro pasos: escanear, modelar, imprimir y limpiar.
A continuación, un análisis más detallado:
1. Escaneando
El proceso comienza con la exploración del miembro patológico. Se trata de posicionar la extremidad y realizar la exploración. El técnico añade los puntos de referencia mientras rectifica la exploración, lo que no suele llevar más de unos minutos. En el caso de ortesis complicadas o miembros con múltiples marcadores, puede llevar algo más de tiempo. Sin embargo, la solución de escaneado en 3D permite una medición más exacta sin las dificultades de los moldes tradicionales.
2. Modelar y modificar
No hay necesidad de yeso, ni de moldes positivos o negativos. Tampoco hay proceso de secado, lo que significa que el técnico pasa menos tiempo esperando. En su lugar, puede pasar directamente al modelado y la modificación de la exploración. El posicionamiento y el esculpido no llevan más de tres minutos. Se puede añadir el relleno o la espuma correspondiente.
3. Impresión
El siguiente paso es el proceso de impresión. Una serie de rayos infrarrojos rápidos determinan el contorno del miembro, sobre el que se puede construir un modelo para la órtesis, utilizando un escáner portátil y una tableta. El proceso de impresión puede durar entre 2 y 24 horas. Esto puede ser largo y quizás sea más largo de lo preferible. Sin embargo, la tecnología de impresión en 3D se está desarrollando rápidamente y podemos esperar que la impresión tarde cada vez menos tiempo en el futuro.
4. Limpieza
Por último, la limpieza después de la impresión lleva unos diez minutos. También se pueden añadir correas de velcro utilizando los lazos a través de las trabillas del cinturón.
¿Qué significa todo esto en la práctica?
Limitaciones de la fabricación manual de ortesis
El proceso de fabricación manual puede durar hasta dos días, incluido el secado. El técnico tiene que dedicar la mayor parte de ese tiempo a trabajar en la órtesis, lo que le resta tiempo al trabajo con los pacientes y a otros aspectos de su trabajo.
La fabricación tradicional también requiere varios materiales diferentes, como la escayola, la espuma de plastaformación y el termoplástico, así como una variedad de herramientas de medición y conformación. Por desgracia, independientemente de los conocimientos y la experiencia de los técnicos ortopédicos, la fabricación manual es propensa a los errores. Cuando se trata de casos más complejos, es posible que haya que volver a empezar el proceso.
Además de todo esto, producir múltiples órtesis personalizadas con la misma calidad es un reto. Para el técnico, esto puede significar un proceso largo y desordenado que necesita mucha planificación y preparación.
El flujo de trabajo en 3D está diseñado para responder a esto.
Cómo la tecnología 3D cambia la fabricación de ortesis
En la práctica, la impresión 3D ofrece un proceso más simplificado y racionalizado para los técnicos ortopédicos. Los técnicos pueden saltarse el paso manualmente intensivo de moldear el yeso y dedicar su tiempo a otras tareas. Esto también significa que, a largo plazo, hay menos necesidad de un gran lugar de trabajo para albergar la maquinaria, las herramientas y todos los modelos de ortesis.
Otro cambio importante es que el escaneo 3D es un método de medición mucho más preciso y exacto. Las imprecisiones cometidas por la impresora 3D son escasas. Además, el almacenamiento digital permite al técnico ortopédico encontrar, modificar y reutilizar toda la información sobre la órtesis de sus pacientes, todo ello sin ocupar espacio y reduciendo considerablemente la cantidad de residuos. Si se necesita un cambio o varias ortesis personalizadas, el técnico puede acceder fácilmente a los datos almacenados y hacer un nuevo modelo simplemente pulsando el botón.
Por último, una solución de impresión 3D puede reducir drásticamente el tiempo dedicado a tareas manuales y repetitivas. Para los técnicos ortopédicos, esto significa más tiempo para centrarse en cada paciente, una comunicación más fácil y grandes posibilidades de producir ortesis que se ajusten perfectamente.
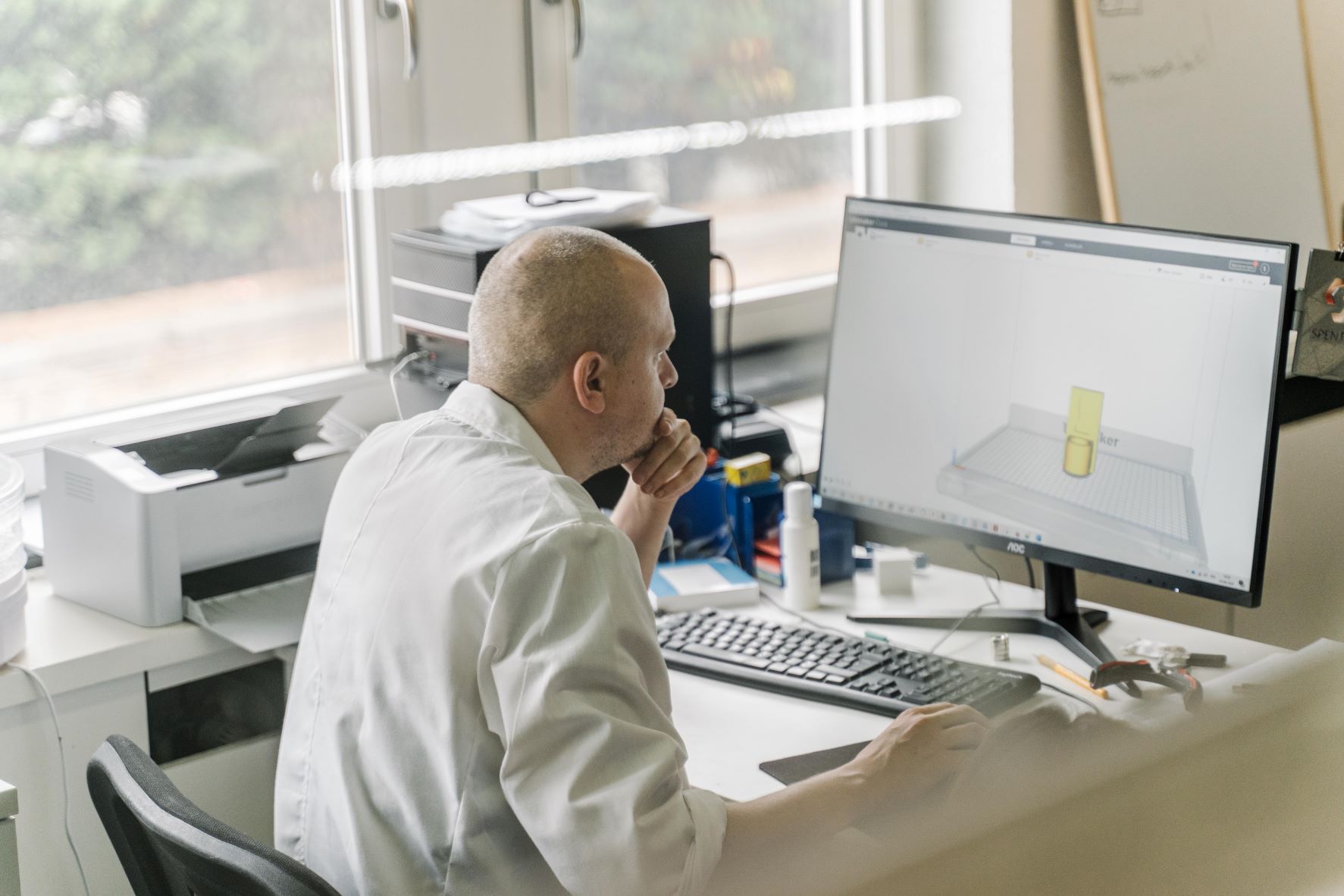
AFOs impresos en 3D
La tecnología ya ha demostrado que aporta un gran valor al campo de la ortopedia, incluidos los AFO. En particular, estudios como el de Cha, Yong Ho y otros muestran el gran potencial de los AFO impresos en 3D tanto para los profesionales como para los pacientes. Otro estudio, realizado por Dal Maso, Alberto y Francesca Cosmi, analizó el procedimiento para diseñar un AFO impreso en 3D totalmente personalizado. El estudio llegó a la conclusión de que el proceso puede automatizarse fácilmente, reduciendo aún más el tiempo y los costes de todo el proceso, a la vez que se obtiene un AFO cómodo y práctico para el paciente.
Quizá la mayor preocupación del flujo de trabajo de la impresión 3D sea el tiempo. Se tarda hasta 24 horas en imprimir la órtesis, lo que puede parecer mucho. Sin embargo, una vez puesta en marcha, la impresora funciona de forma autónoma, sin necesidad de un operario. Por término medio, sólo se necesitan 10 minutos para modelar el AFO. En las 24 horas que dura el proceso, esto significa que sólo el 0,5% de la producción requiere una intervención humana real.
Aunque la fusión de la tecnología 3D con la ortopedia puede parecer desalentadora para el técnico ortopédico, tiene muchas ventajas. El objetivo de esta tecnología no es sustituir el trabajo y la experiencia de los técnicos, sino hacer que su trabajo tenga más sentido y sea más eficiente. Les da más tiempo para centrarse en los pacientes y desarrollar soluciones para ellos, en lugar de dedicar tiempo a tareas repetitivas o a la administración.
En Spentys, hemos lanzado recientemente una nueva función como parte de nuestro software, adaptada específicamente para el diseño y la fabricación de AFO. No necesita ningún conocimiento técnico previo para utilizar nuestra plataforma y le guiaremos durante todo el proceso, asegurándonos de que se adapte a su flujo de trabajo habitual.
Comience por reservar su llamada con un especialista hoy mismo.